The recent Techtextil show in Frankfurt once again emphasised the sheer diversity of applications for nonwovens and technical textiles, according to finishing technology specialist Monforts.
“We fielded enquiries at top management level from an extremely wide range of companies, all with very different ideas for new product applications during the show,” said Alexander Fitz, who joined the company a year ago as engineer for textile technologies and co-ordinator of the Monforts Advanced Technology Centre (ATC).
Fitz brings a solid background in both technical textile technology and processes to the role, having previously worked for both a well-known nonwovens machinery builder and a leading roll-goods manufacturer.
Trials
“We are now looking forward to interesting new trials and pilot production runs, as well as the commissioning of new orders for machines resulting from the extremely busy exhibition,” he says. “Obviously, everyone at the moment is looking to make energy savings, and we have developed a range of options for helping companies increase their resource efficiency, both on new lines and as retrofitted systems, but this is not stifling innovation at the new material level.
“There was a lot of interest in what is possible with the Montex®Coat coating system and the range of different techniques it enables, and at our ATC in Mönchengladbach, a Montex®Coat unit is integrated into the full technical textiles pilot line, on which it is possible to run new fabrics in widths of up to 1.8 metres.”
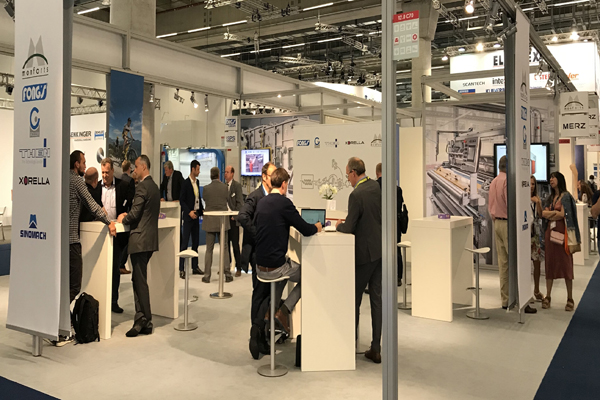
Explosion proof
The technical textiles line at the ATC incorporates a Montex four-chamber stenter and is fitted with an explosion-proof coating application chamber in order to allow treatment to be carried out with organic solvents and other volatile materials.
Every single component within the chamber has to meet the standards of the European Union’s ATEX directives for working in a potentially explosive atmosphere. A range of sensors linked to alarms operate at various levels within the chamber to ensure the specified lower explosion limit (LOL) is never exceeded and the ventilation adapts accordingly.
Advanced functions
Special features on the finishing line relate to further advanced functions such as the ability to treat materials not only at temperatures of up to 320°C, but also to be able to treat the top and bottom faces of certain materials at different temperatures within a single pass through the machine.
To achieve this, the first two chambers of the stenter are fitted with special, heavy duty TwinAir ventilation motors and separate burners for individual top/bottom temperature. A temperature differential of up to 60°C can be achieved between the upper and lower nozzles within the chamber, depending on the treatment paramenters.
“There are many applications where employing two separate temperature treatments is beneficial, such as floorcoverings – where the textile face fabric is treated at one temperature and the rubber backing at another – as well as PVC flooring employing chemical foams or for materials like black-out roller blinds with heavy backings,” Fitz explains. “Other materials, such as PTFE-coated filter materials are also applied and then cured at separate temperatures.”
Another key feature of the technical textiles line at the ATC is the special stretching device which is capable of pulling ten tons in length and ten tons in width – a huge amount per square metre of fabric and necessary in the production of materials such as woven or 3D knits for high temperature filter media.
“This line has been engineered to provide the ultimate in precision coating and finishing for industrial-scale trials and we are greatly looking forward to the new work that will be conducted following our discussions with companies at Techtextil,” Fitz concludes.